Apollo DFT - Structural Steel Tubes
Apollo DFT - Structural Steel Tubes
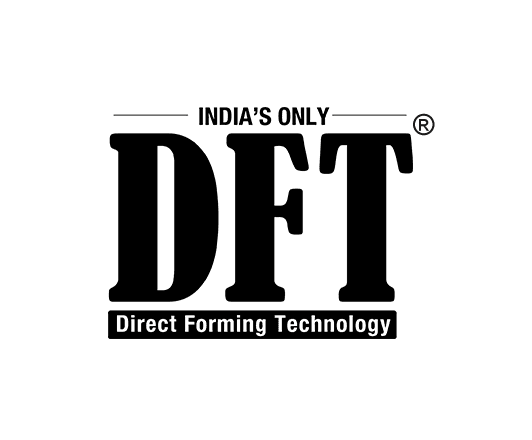
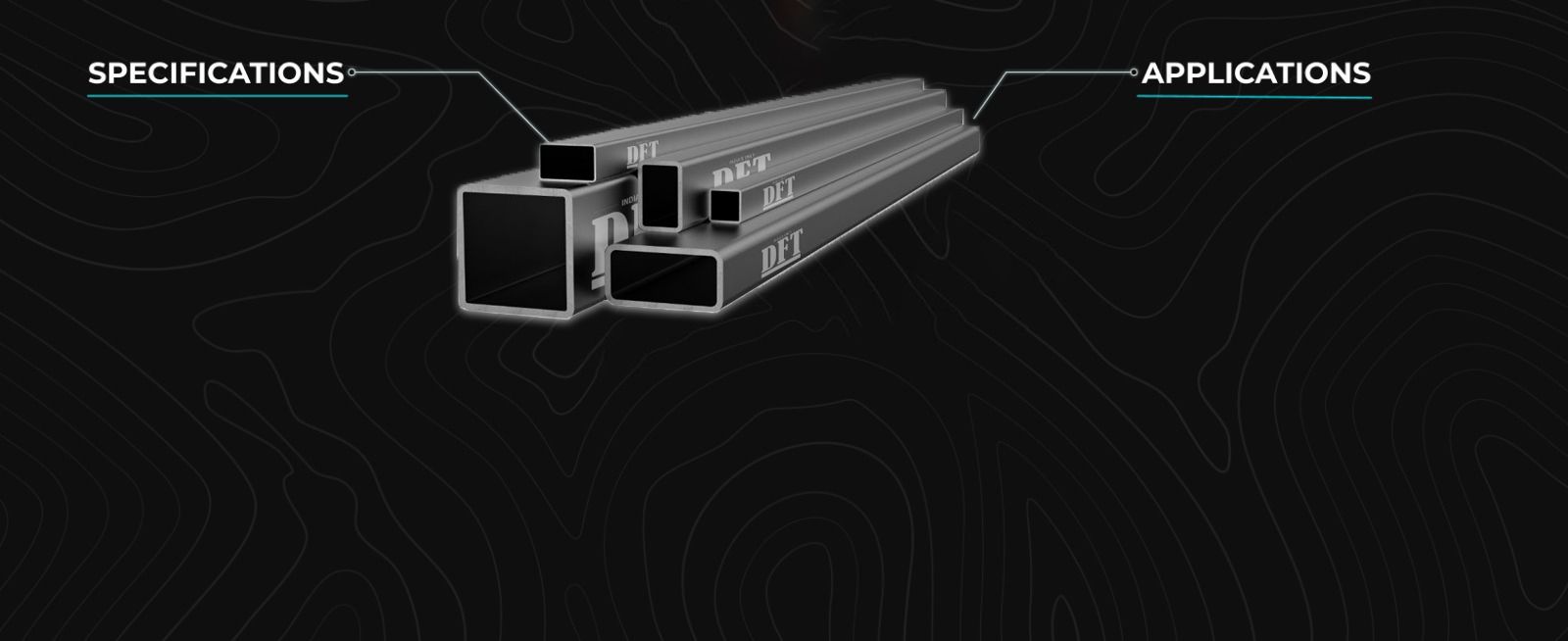
Product Range: 12mm x 12mm to 300mm x 300mm
Thickness: 1mm to 12mm
Rectangular Hollow Section (RHS)
Product Range:26mm x 13mm to 400mm to 200mm
Thickness:1mm to 12mm
Circular Hollow Section (CHS)
Product Range: 21.3 mm to 355.6 mm
Thickness:1mm to 10 mm
BRAND PERSONALITY OF APOLLO DFT
- Lightweight, strong, and versatile Apollo DFT is ideal for application across segments, be it residential, commercial, or infrastructure projects. The superior quality product comes with a customizable size option to meet specific requirements.
ABOUT APOLLO DFT
- This technology opens a new era in structural steel tube production. The use of Direct Forming Technology (DFT) is pioneered by APL Apollo in India and is the only company using this high-tech production methodology in the most elaborate manner that also covers structural steel tubes, (ERW) electric resistance welding tubes, square tubes, rectangular tubes and more.
- The DFT system is the result of many years of experience and knowledge in the structural steel tube field. This method brings undisputed advantages in terms of flexibility, production capability, and cost reduction. This innovation enables the possibility to produce any size, included in the mill range, without roll change, resulting in an extreme reduction in setup time.
ADVANTAGES OF APOLLO (DFT) DIRECT FORMING TECHNOLOGY
- Direct material saving of 2% to 10% depending upon specifications, size, and thickness as compared to tubes manufactured by conventional technology & results in seamless welding.
- The physical and Theoretical weight of the tubes will be the same, as per IS 4923.
- Corner radius are sharp, uniform and aesthetically looks good
- Odd sizes (any size can be rolled out subject to minimum order quantity)
- Short delivery period
- The combination of ERW tubes, structural steel tubes and DFT is a game changer and makes APL Apollo a trustworthy steel manufacturer in India
- DFT is a new approach for producing tubes. This method allows for the production of bespoke hollow sections by including them in the mill range without modifying the roll.
OTHER APPLICATIONS OF APL (DFT) DIRECT FORMING TECHNOLOGY
Tubular Connection: DFT study of tubular connection is:
WELDED AND BOLTED CONNECTION: Beams and columns are usually connected on-site by bolting. In the case of a Rectangular Hollow Section (RHS) beam connection to an l-section column, a welded extended end-plate to the beam permits the use of a conventional bolted connection to the column flange or web. The bolts may be countersunk into the thick end plate if the connection is important visually. A number of typical simple connections using cleats welded to an RHS column show a fin plate welded to the face of the column and the supporting bracket can be detailed to be visually interesting.
COLUMN BASES: Bases to tubular columns take two basic forms: Pinned and Rigged. The details are employed to reflect the transfer of forces and moments. A genuine pinned connection can be achieved by a single pin from the projecting plate.
WELDED FINS: Fins or brackets may be welded to the side of the Circular Hollow Section (CHS) or (SHS) Square hollow section/(RHS) Rectangular hollow section to provide direct attachment of secondary members. Connections of this type require careful design because of the possible local distortion of the walls of larger hollow sections. Alternatively, welded threaded studs with extended washers may be used to attach the purlins to the section. The attachment of tension ties or rod-bracing members requires similar details. High local forces from ties may also be transferred by ‘patch-type’ connections, which may be profiled around the circular section so that weld forces are transferred smoothly to the walls of the section. Multiple welded fin connections have been used successfully on a number of major projects.
REINFORCEMENT CONNECTIONS: For maximum resistance of the members, it is usually more efficient to select larger tubular sections with thin walls. However, when designing the connections, it is more advantageous to use chord members that are thicker and smaller in section (provided that they are not smaller than the bracing members). Therefore, a compromise is necessary for overall design and fabrication efficiency. In some cases, connections may have to be strengthened locally to resist the applied forces, if it is not possible to increase the member size or thickness. This can be achieved by welding plates to the chord face. It should also be noted that overlaps will also increase connection resistance, especially for RHS members. When a third member is required at the intersection, a ‘T’ piece can also be used. Other non-standard stiffened K connections can be used to increase the load capacity of the connection.
BENEFITS OF DIRECT FORMING TECHNOLOGY (DFT)
- Perfect hollow sections for all your construction needs.
- Customized sizes
- Greater flexibility
- Modify tube dimensions
- Saves time
- Material saving
- Alterable corner radius
- Uniform width throughout the tube/pipe
USE OF APOLLO DFT IN INFRASTRUCTURE
- Kempegowda International Airport: This is constructing a garden terminal called T2 to accommodate the increasing passenger traffic. The contractor had the requirement of hollow sections 350 mm x 250 mm x 10 mm. APL APOLLO was able to provide the required sizes and quantities within 7 days of issuing the purchase order. APL Apollo has the technology to service customized sizes in a minimum lead time. This was possible because of DFT (Direct Forming Technology) which is connected only with APL APOLLO in India. This technology helps in giving customized sizes more exceptional flexibility and minimum lead time.
- Kartarpur Corridor Gurudwara: The contractors approached APL Apollo Tubes and requested to supply the required structural steel tubes and pipes in the given time frame. APL Apollo supplied approximately 500 Tons out of the total requirement of 615 Tons within 7 days of LOI. With APL Apollo Tubes’ flexibility on sizes and proximity of plant locations, the company was able to complete the project with great precision.
FEATURES OF APOLLO DFT
- DFT produces rectangular and square hollow sections that are lesser in weight and superior in strength as compared to conventional methods of steel.
- APL Apollo gets the widest range with structural steel tubes and DFT. The production units are equipped to customize and deliver special requirements in terms of size, quantity or surface finish that are beyond the standard requirements of the industry as per the needs of customers.
WHY IS APOLLO DFT REQUIRED?
APL Apollo DFT finds applications in various industries due to its sheer versatility. From architecture to various industries, agriculture to general engineering, with the help of new-age technology; Direct Forming Technology has been shaping the nation& infrastructure.
APL Apollo is the right choice for all steel structures, PEB structures, structural steel buildings, and construction.